Łączenie dwóch kompresorów to proces, który może znacząco zwiększyć wydajność systemu pneumatycznego. Przede wszystkim należy zrozumieć, jakie są cele takiego połączenia. W przypadku, gdy potrzebujemy większej mocy lub chcemy zredukować czas pracy urządzeń, łączenie kompresorów może być idealnym rozwiązaniem. Ważne jest, aby przed przystąpieniem do jakichkolwiek działań zaplanować cały proces. Należy uwzględnić typy kompresorów, które chcemy połączyć, ponieważ różne modele mogą wymagać różnych podejść do instalacji. Istotnym krokiem jest również dobór odpowiednich rur i złączek, które będą w stanie wytrzymać ciśnienie generowane przez oba urządzenia. Warto również rozważyć zastosowanie zaworów zwrotnych, które zapobiegną cofaniu się powietrza w systemie. Kolejnym aspektem jest odpowiednie umiejscowienie kompresorów, aby zapewnić ich efektywne chłodzenie oraz dostęp do konserwacji.
Jakie są zalety łączenia dwóch kompresorów?
Łączenie dwóch kompresorów niesie ze sobą szereg korzyści, które mogą znacznie poprawić funkcjonalność całego systemu pneumatycznego. Przede wszystkim zwiększa to wydajność produkcji powietrza, co jest kluczowe w wielu branżach przemysłowych. Dzięki temu można uniknąć sytuacji, w której jeden kompresor pracuje na granicy swoich możliwości, co mogłoby prowadzić do jego szybszego zużycia lub awarii. Połączenie dwóch jednostek umożliwia także lepsze zarządzanie obciążeniem, co przekłada się na dłuższą żywotność sprzętu. Dodatkowo, w przypadku awarii jednego z kompresorów, drugi może przejąć jego funkcje, co zwiększa niezawodność całego systemu. Warto również zauważyć, że połączenie kompresorów może przyczynić się do oszczędności energii poprzez optymalizację pracy urządzeń.
Jakie są najważniejsze kroki przy łączeniu kompresorów?
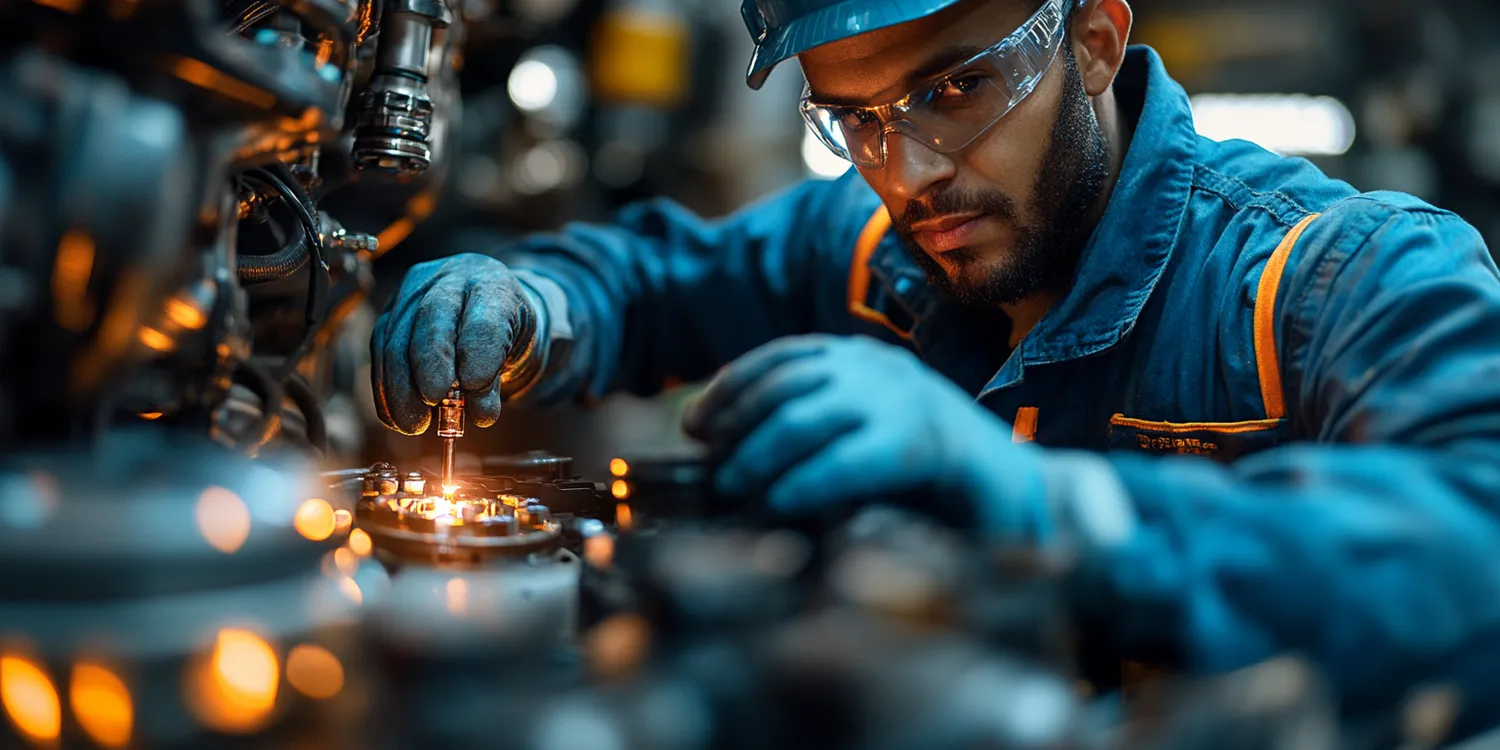
Aby skutecznie połączyć dwa kompresory, należy przejść przez kilka kluczowych kroków, które zapewnią prawidłowe funkcjonowanie całego systemu. Pierwszym krokiem jest dokładne zaplanowanie układu instalacji oraz wybór odpowiednich komponentów. Należy zwrócić uwagę na parametry techniczne obu kompresorów oraz ich kompatybilność. Kolejnym istotnym etapem jest przygotowanie miejsca na instalację – powinno być ono dobrze wentylowane oraz łatwo dostępne dla serwisu. Następnie należy zainstalować odpowiednie rury i złączki, dbając o to, aby były one dostosowane do ciśnienia roboczego urządzeń. Ważne jest także zamontowanie zaworów zwrotnych oraz filtrów powietrza, które zabezpieczą system przed zanieczyszczeniami i nadmiernym ciśnieniem. Po zakończeniu montażu warto przeprowadzić testy szczelności oraz sprawdzić działanie obu kompresorów w trybie współpracy.
Jakie problemy mogą wystąpić podczas łączenia kompresorów?
Podczas łączenia dwóch kompresorów mogą wystąpić różnorodne problemy techniczne oraz operacyjne, które warto mieć na uwadze przed rozpoczęciem prac instalacyjnych. Jednym z najczęstszych problemów jest niewłaściwe dobranie urządzeń o różnych parametrach technicznych, co może prowadzić do nierównomiernego obciążenia i szybszego zużycia jednego z nich. Innym zagrożeniem jest nieodpowiednia instalacja rur i złączek, co może skutkować wyciekami powietrza i obniżeniem efektywności całego systemu. Ponadto brak zaworów zwrotnych może prowadzić do cofania się powietrza i uszkodzenia kompresora. Warto również pamiętać o konieczności regularnej konserwacji obu urządzeń – zaniedbania w tym zakresie mogą prowadzić do awarii oraz kosztownych napraw. Problemy mogą także wynikać z niewłaściwego umiejscowienia kompresorów; jeśli nie będą one miały zapewnionej odpowiedniej wentylacji lub przestrzeni roboczej, ich wydajność może ulec znacznemu pogorszeniu.
Jakie narzędzia są potrzebne do połączenia kompresorów?
Aby skutecznie połączyć dwa kompresory, niezbędne jest przygotowanie odpowiednich narzędzi oraz materiałów, które umożliwią przeprowadzenie prac instalacyjnych. Przede wszystkim warto zaopatrzyć się w zestaw podstawowych narzędzi ręcznych, takich jak klucze płaskie i nasadowe, śrubokręty oraz szczypce. W przypadku instalacji rur pneumatycznych przydatne będą także narzędzia do cięcia i gięcia rur, które pozwolą na precyzyjne dopasowanie elementów systemu. Dodatkowo, warto mieć pod ręką wkrętarkę elektryczną, która znacznie przyspieszy proces montażu. W zależności od wybranego systemu połączeń, mogą być potrzebne także specjalistyczne narzędzia do montażu złączek i zaworów. Oprócz narzędzi, istotne jest również zgromadzenie odpowiednich materiałów, takich jak rury, złączki, zawory zwrotne oraz filtry powietrza. Warto również zaopatrzyć się w uszczelki oraz taśmy teflonowe, które pomogą zapewnić szczelność połączeń.
Jakie są różnice między kompresorami tłokowymi a śrubowymi?
Wybór odpowiednich kompresorów do połączenia często sprowadza się do decyzji pomiędzy kompresorami tłokowymi a śrubowymi. Kompresory tłokowe działają na zasadzie zmiany objętości powietrza w cylindrze za pomocą ruchomego tłoka. Charakteryzują się one prostą konstrukcją oraz niższymi kosztami zakupu, co czyni je popularnym wyborem w małych warsztatach czy gospodarstwach domowych. Z drugiej strony, kompresory śrubowe są bardziej zaawansowane technologicznie i oferują wyższą wydajność oraz ciągłość pracy. Ich działanie opiera się na sprężaniu powietrza za pomocą dwóch wirujących śrub, co pozwala na uzyskanie stabilnego ciśnienia roboczego przez dłuższy czas. Kompresory śrubowe są zazwyczaj cichsze i bardziej energooszczędne niż ich tłokowe odpowiedniki, co czyni je idealnym rozwiązaniem dla przemysłu. Warto również zauważyć, że kompresory śrubowe wymagają regularnej konserwacji oraz smarowania, co może wiązać się z dodatkowymi kosztami eksploatacyjnymi.
Jakie są najlepsze praktyki przy łączeniu kompresorów?
Podczas łączenia dwóch kompresorów warto przestrzegać kilku najlepszych praktyk, które pomogą zapewnić efektywność i bezpieczeństwo całego systemu. Przede wszystkim należy dokładnie zaplanować cały proces instalacji, uwzględniając wszystkie aspekty techniczne oraz operacyjne. Ważne jest także przeprowadzenie analizy potrzeb dotyczących wydajności powietrza oraz ciśnienia roboczego, aby dobrać odpowiednie urządzenia. Kolejnym krokiem jest staranne wykonanie wszystkich połączeń – należy upewnić się, że rury i złączki są odpowiednio zamontowane i szczelne, aby uniknąć wycieków powietrza. Regularne monitorowanie stanu technicznego obu kompresorów jest kluczowe dla ich długotrwałej eksploatacji; warto prowadzić dziennik serwisowy oraz notować wszelkie awarie czy przestoje. Dobrze jest również przeprowadzać okresowe przeglądy techniczne oraz konserwacje zgodnie z zaleceniami producenta.
Jakie zastosowania mają połączone kompresory w przemyśle?
Połączone kompresory znajdują szerokie zastosowanie w różnych branżach przemysłowych, gdzie wymagane jest dostarczanie dużych ilości sprężonego powietrza. W przemyśle budowlanym często wykorzystuje się je do zasilania narzędzi pneumatycznych, takich jak młoty udarowe czy wiertarki. Dzięki zwiększonej wydajności połączonych jednostek możliwe jest jednoczesne korzystanie z wielu narzędzi bez obawy o spadek ciśnienia roboczego. W sektorze produkcyjnym połączone kompresory mogą wspierać linie montażowe oraz maszyny automatyczne, co przyczynia się do zwiększenia efektywności produkcji. W branży motoryzacyjnej sprężone powietrze jest wykorzystywane do malowania samochodów oraz obsługi różnych procesów technologicznych. Połączenie dwóch kompresorów może również znaleźć zastosowanie w systemach klimatyzacyjnych i wentylacyjnych, gdzie wymagana jest stała dostawa sprężonego powietrza do chłodzenia lub ogrzewania pomieszczeń.
Jakie są koszty związane z łączeniem kompresorów?
Koszty związane z łączeniem dwóch kompresorów mogą być różnorodne i zależą od wielu czynników, takich jak typ urządzeń, materiały użyte do instalacji czy dodatkowe komponenty wymagane do prawidłowego funkcjonowania systemu. Na początku warto uwzględnić koszty zakupu samych kompresorów; ceny mogą się znacznie różnić w zależności od ich mocy i technologii wykonania. Następnie należy doliczyć wydatki związane z materiałami instalacyjnymi, takimi jak rury pneumatyczne, złączki czy zawory zwrotne. Koszt robocizny również powinien być uwzględniony – jeśli planujemy zatrudnienie specjalisty do przeprowadzenia montażu, warto wcześniej ustalić stawki za usługi hydrauliczne lub pneumatyczne. Dodatkowo należy pamiętać o przyszłych kosztach eksploatacyjnych związanych z konserwacją obu urządzeń; regularna obsługa techniczna może wiązać się z dodatkowymi wydatkami na części zamienne czy smary.