Budowa maszyn pneumatycznych opiera się na kilku kluczowych elementach, które współpracują ze sobą, aby zapewnić efektywne działanie systemów pneumatycznych. Wśród najważniejszych komponentów znajdują się sprężarki powietrza, które odpowiadają za wytwarzanie sprężonego powietrza. Sprężarki te mogą być różnego rodzaju, w tym tłokowe, śrubowe czy wirnikowe, a ich wybór zależy od specyfiki zastosowania oraz wymagań dotyczących ciśnienia i wydajności. Kolejnym istotnym elementem są zawory, które kontrolują przepływ powietrza w systemie. Zawory te mogą być ręczne lub automatyczne, a ich odpowiedni dobór jest kluczowy dla sprawności całego układu. Rury i przewody pneumatyczne również odgrywają ważną rolę, ponieważ transportują sprężone powietrze do różnych części maszyny. Dodatkowo, siłowniki pneumatyczne przekształcają energię sprężonego powietrza w ruch mechaniczny, co jest niezbędne do wykonywania różnych zadań.
Jakie są zalety i wady budowy maszyn pneumatycznych
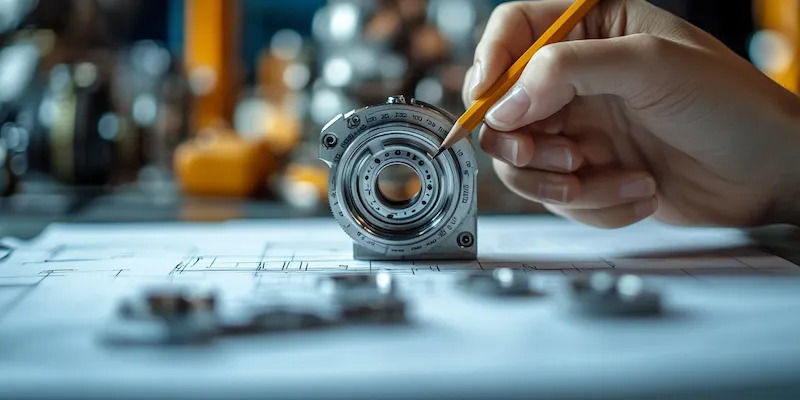
Budowa maszyn pneumatycznych niesie ze sobą szereg zalet oraz wad, które warto rozważyć przed podjęciem decyzji o ich zastosowaniu. Do głównych zalet należy zaliczyć prostotę konstrukcji oraz łatwość w obsłudze. Systemy pneumatyczne są zazwyczaj mniej skomplikowane niż hydrauliczne czy elektryczne, co ułatwia ich serwisowanie oraz naprawy. Ponadto maszyny pneumatyczne charakteryzują się dużą elastycznością i wszechstronnością zastosowań, co sprawia, że znajdują zastosowanie w wielu branżach przemysłowych. Ich działanie jest również stosunkowo ciche w porównaniu do innych systemów napędowych. Z drugiej strony istnieją pewne wady związane z budową maszyn pneumatycznych. Przede wszystkim efektywność energetyczna takich systemów może być niższa niż w przypadku innych technologii, co prowadzi do wyższych kosztów eksploatacji. Dodatkowo sprężone powietrze może być źródłem problemów związanych z wyciekami oraz koniecznością regularnego monitorowania ciśnienia i jakości powietrza.
Jakie są zastosowania maszyn pneumatycznych w przemyśle
Maszyny pneumatyczne znajdują szerokie zastosowanie w różnych dziedzinach przemysłu dzięki swojej wszechstronności oraz efektywności działania. W przemyśle produkcyjnym często wykorzystuje się je do automatyzacji procesów montażowych oraz pakowania produktów. Siłowniki pneumatyczne umożliwiają szybkie i precyzyjne ruchy, co znacząco zwiększa wydajność linii produkcyjnych. W branży motoryzacyjnej maszyny pneumatyczne są wykorzystywane do malowania pojazdów oraz jako narzędzia do obróbki metali, takie jak młoty czy wiertarki pneumatyczne. W logistyce i magazynowaniu systemy pneumatyczne służą do transportu materiałów oraz automatyzacji procesów załadunku i rozładunku towarów. W sektorze spożywczym maszyny te pomagają w pakowaniu żywności oraz utrzymywaniu higienicznych warunków pracy dzięki możliwości łatwego czyszczenia komponentów. Ponadto coraz częściej wykorzystuje się je w branży medycznej do napędu urządzeń diagnostycznych oraz chirurgicznych.
Jakie innowacje wpływają na rozwój budowy maszyn pneumatycznych
Rozwój technologii ma znaczący wpływ na budowę maszyn pneumatycznych, a innowacje w tej dziedzinie przyczyniają się do poprawy ich wydajności oraz funkcjonalności. Jednym z najważniejszych trendów jest automatyzacja procesów produkcyjnych poprzez integrację systemów pneumatycznych z nowoczesnymi rozwiązaniami informatycznymi i sztuczną inteligencją. Dzięki temu możliwe jest monitorowanie pracy maszyn w czasie rzeczywistym oraz optymalizacja ich działania na podstawie zebranych danych. Kolejnym istotnym kierunkiem rozwoju jest miniaturyzacja komponentów pneumatycznych, co pozwala na tworzenie bardziej kompaktowych i lekkich urządzeń, które można łatwo integrować z innymi systemami technologicznymi. Innowacje dotyczą także materiałów używanych do produkcji elementów maszyn pneumatycznych; nowe kompozyty i stopy metali zwiększają odporność na zużycie oraz korozję, co przekłada się na dłuższą żywotność urządzeń. Dodatkowo rozwijane są technologie związane z odzyskiem energii ze sprężonego powietrza, co przyczynia się do zwiększenia efektywności energetycznej całych systemów.
Jakie są kluczowe zasady projektowania maszyn pneumatycznych
Projektowanie maszyn pneumatycznych wymaga uwzględnienia szeregu kluczowych zasad, które mają na celu zapewnienie ich efektywności oraz bezpieczeństwa użytkowania. Przede wszystkim, należy dokładnie określić wymagania dotyczące ciśnienia i przepływu powietrza, co pozwoli na odpowiedni dobór komponentów. Warto również zwrócić uwagę na ergonomię i łatwość obsługi, co jest szczególnie istotne w kontekście długotrwałego użytkowania maszyn przez operatorów. Kolejnym ważnym aspektem jest dobór materiałów, które powinny charakteryzować się wysoką odpornością na zużycie oraz korozję, co wydłuży żywotność urządzenia. Należy także pamiętać o odpowiedniej wentylacji oraz systemach chłodzenia, które zapobiegają przegrzewaniu się komponentów podczas intensywnej pracy. Projektując maszyny pneumatyczne, warto również uwzględnić możliwość łatwego dostępu do elementów serwisowych, co ułatwi konserwację i naprawy.
Jakie są najczęstsze problemy związane z maszynami pneumatycznymi
Maszyny pneumatyczne, mimo swoich licznych zalet, mogą napotykać różnorodne problemy w trakcie eksploatacji. Jednym z najczęstszych problemów są wycieki sprężonego powietrza, które mogą prowadzić do utraty efektywności całego systemu oraz zwiększenia kosztów eksploatacji. Wyciek może występować w miejscach połączeń rur i przewodów lub w uszczelkach siłowników. Innym powszechnym problemem jest niewłaściwe ciśnienie robocze, które może wynikać z błędnego ustawienia zaworów lub uszkodzenia sprężarki. Niewłaściwe ciśnienie wpływa negatywnie na wydajność maszyny oraz może prowadzić do jej uszkodzenia. Dodatkowo, zanieczyszczenia w sprężonym powietrzu mogą powodować awarie komponentów pneumatycznych; dlatego tak ważne jest stosowanie filtrów i osuszaczy. Problemy mogą również wynikać z niewłaściwego serwisowania maszyn; brak regularnej konserwacji prowadzi do szybszego zużycia części oraz zwiększa ryzyko awarii.
Jakie są przyszłe kierunki rozwoju technologii maszyn pneumatycznych
Przyszłość technologii maszyn pneumatycznych zapowiada się obiecująco dzięki ciągłemu rozwojowi innowacyjnych rozwiązań oraz rosnącemu zainteresowaniu automatyzacją procesów przemysłowych. Jednym z kluczowych kierunków rozwoju jest integracja systemów pneumatycznych z technologią Internetu Rzeczy (IoT), co umożliwi monitorowanie i zarządzanie pracą maszyn w czasie rzeczywistym. Dzięki temu możliwe będzie zbieranie danych dotyczących wydajności oraz stanu technicznego urządzeń, co pozwoli na szybsze wykrywanie usterek i optymalizację procesów produkcyjnych. Kolejnym istotnym trendem jest rozwój materiałów kompozytowych oraz nanotechnologii, które mogą przyczynić się do poprawy wydajności i trwałości komponentów pneumatycznych. Innowacje te pozwolą na tworzenie lżejszych i bardziej odpornych na zużycie elementów maszyn. Dodatkowo rośnie znaczenie efektywności energetycznej; przyszłe rozwiązania będą skupiały się na minimalizacji strat energii oraz wykorzystaniu odnawialnych źródeł energii do napędu systemów pneumatycznych.
Jakie są różnice między systemami pneumatycznymi a hydraulicznymi
Systemy pneumatyczne i hydrauliczne to dwa różne podejścia do przenoszenia energii mechanicznej, które mają swoje unikalne cechy oraz zastosowania. Główna różnica między nimi polega na medium roboczym; w systemach pneumatycznych wykorzystuje się sprężone powietrze, podczas gdy w hydraulicznych stosuje się cieczy hydrauliczne. To sprawia, że maszyny pneumatyczne są zazwyczaj lżejsze i bardziej mobilne niż hydrauliczne, co czyni je idealnymi do zastosowań wymagających dużej elastyczności. Z drugiej strony systemy hydrauliczne oferują większą moc i precyzję działania; dlatego często znajdują zastosowanie w ciężkim przemyśle oraz w maszynach budowlanych. Ponadto systemy hydrauliczne mogą działać przy znacznie wyższych ciśnieniach niż pneumatyczne, co pozwala na przenoszenie większych obciążeń. W kwestii kosztów eksploatacji systemy pneumatyczne są zazwyczaj tańsze w utrzymaniu ze względu na prostszą konstrukcję oraz mniejsze ryzyko wycieków. Jednakże w przypadku aplikacji wymagających dużej siły czy precyzyjnego sterowania lepszym wyborem mogą być systemy hydrauliczne.
Jakie są najlepsze praktyki w zakresie konserwacji maszyn pneumatycznych
Aby zapewnić długotrwałe i efektywne działanie maszyn pneumatycznych, konieczne jest przestrzeganie najlepszych praktyk w zakresie ich konserwacji. Regularna kontrola stanu technicznego komponentów to kluczowy element utrzymania sprawności urządzeń; należy regularnie sprawdzać szczelność połączeń oraz stan uszczelek i filtrów powietrza. Warto także monitorować poziom oleju w sprężarkach oraz jego jakość; zanieczyszczony olej może prowadzić do uszkodzeń silnika sprężarki oraz obniżenia wydajności całego układu. Kolejnym istotnym aspektem jest czyszczenie filtrów powietrza i osuszaczy; ich regularna wymiana lub czyszczenie zapobiega przedostawaniu się zanieczyszczeń do układu pneumatycznego. Należy również dbać o odpowiednią temperaturę pracy urządzeń; przegrzewanie się komponentów może prowadzić do ich szybszego zużycia lub awarii. Warto także prowadzić dokumentację serwisową, która pomoże śledzić historię konserwacji oraz ewentualnych napraw maszyn.
Jakie są najważniejsze trendy w dziedzinie budowy maszyn pneumatycznych
W dziedzinie budowy maszyn pneumatycznych można zaobserwować kilka istotnych trendów, które kształtują przyszłość tej technologii. Przede wszystkim rośnie znaczenie automatyzacji procesów przemysłowych; coraz więcej producentów wdraża rozwiązania umożliwiające integrację systemów pneumatycznych z robotyką i sztuczną inteligencją. Dzięki temu możliwe jest zwiększenie wydajności produkcji oraz redukcja błędów ludzkich podczas obsługi maszyn. Kolejnym ważnym trendem jest rozwój technologii 3D drukowania komponentów pneumatycznych; ta innowacyjna metoda produkcji pozwala na szybkie prototypowanie oraz dostosowywanie części do indywidualnych potrzeb klientów. Zwiększa to elastyczność produkcji i skraca czas realizacji zamówień. Dodatkowo rośnie zainteresowanie ekologicznymi rozwiązaniami; producenci starają się opracowywać maszyny o niższym zużyciu energii oraz mniejszym wpływie na środowisko naturalne poprzez zastosowanie materiałów biodegradowalnych czy recyklingowanych.