Przemysł 4.0 to termin, który odnosi się do czwartej rewolucji przemysłowej, charakteryzującej się integracją nowoczesnych technologii w procesach produkcyjnych. Wprowadzenie zaawansowanych systemów automatyzacji, sztucznej inteligencji oraz Internetu Rzeczy (IoT) ma na celu zwiększenie efektywności i elastyczności produkcji. Dzięki tym innowacjom przedsiębiorstwa mogą lepiej dostosować się do zmieniających się potrzeb rynku oraz poprawić jakość swoich produktów. W ramach Przemysłu 4.0 następuje również rozwój inteligentnych fabryk, które wykorzystują dane w czasie rzeczywistym do optymalizacji procesów produkcyjnych. Przykładem może być zastosowanie robotów współpracujących, które pracują obok ludzi, zwiększając wydajność i bezpieczeństwo pracy. Warto zauważyć, że transformacja ta nie dotyczy tylko dużych korporacji, ale także małych i średnich przedsiębiorstw, które mogą korzystać z dostępnych technologii w celu poprawy swojej konkurencyjności na rynku.
Jakie technologie są kluczowe dla Przemysłu 4.0
W kontekście Przemysłu 4.0 kluczowe znaczenie mają różnorodne technologie, które wspierają automatyzację i cyfryzację procesów produkcyjnych. Do najważniejszych z nich należy sztuczna inteligencja, która umożliwia analizę dużych zbiorów danych i podejmowanie decyzji na podstawie uzyskanych informacji. Dzięki AI firmy mogą przewidywać awarie maszyn, co pozwala na minimalizację przestojów i zwiększenie efektywności produkcji. Kolejną istotną technologią jest Internet Rzeczy, który umożliwia komunikację między urządzeniami oraz zbieranie danych w czasie rzeczywistym. Dzięki IoT przedsiębiorstwa mogą monitorować swoje zasoby oraz procesy produkcyjne zdalnie, co przyczynia się do lepszego zarządzania i optymalizacji kosztów. Również technologia blockchain zyskuje na znaczeniu w kontekście Przemysłu 4.0, ponieważ zapewnia bezpieczeństwo transakcji oraz transparentność w łańcuchu dostaw. Dodatkowo rozwój robotyki oraz druku 3D otwiera nowe możliwości w zakresie produkcji niestandardowych produktów oraz personalizacji oferty dla klientów.
Jakie korzyści przynosi wdrożenie Przemysłu 4.0
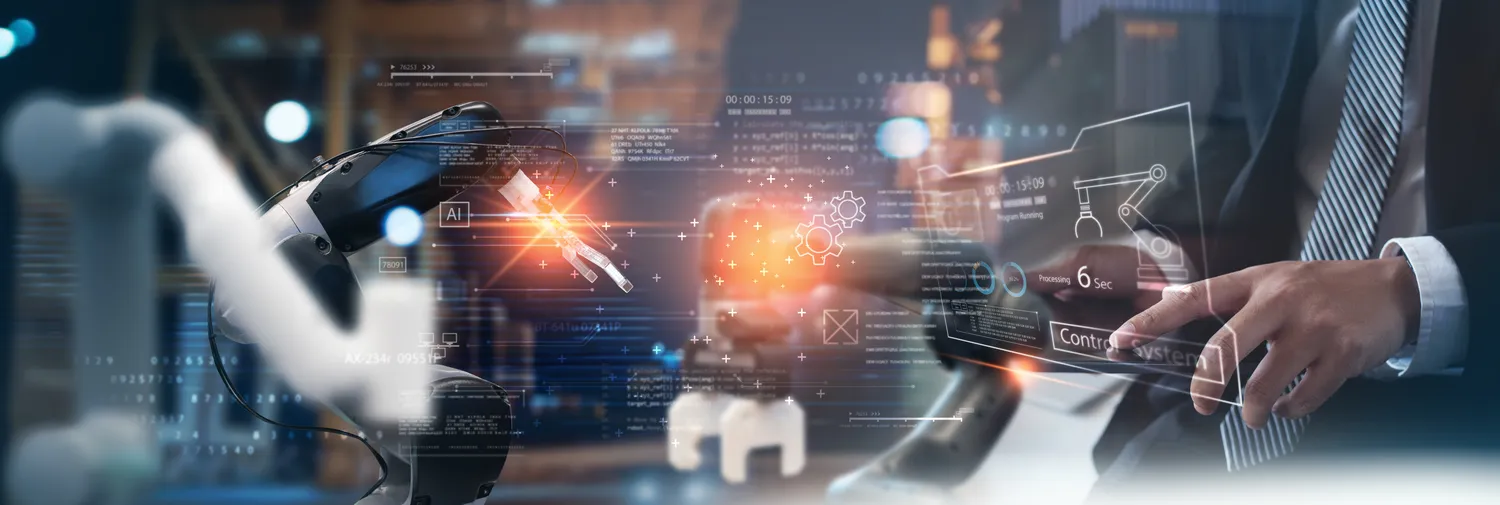
Wdrożenie rozwiązań związanych z Przemysłem 4.0 niesie ze sobą szereg korzyści dla przedsiębiorstw działających w różnych branżach. Po pierwsze, dzięki automatyzacji procesów produkcyjnych możliwe jest znaczne zwiększenie wydajności pracy oraz redukcja kosztów operacyjnych. Firmy mogą szybciej reagować na zmiany popytu oraz dostosowywać swoje linie produkcyjne do aktualnych potrzeb rynku, co przekłada się na większą elastyczność i konkurencyjność. Po drugie, zastosowanie nowoczesnych technologii pozwala na poprawę jakości produktów poprzez precyzyjne monitorowanie procesów oraz eliminację błędów ludzkich. Ponadto, dzięki analizie danych w czasie rzeczywistym przedsiębiorstwa mogą podejmować bardziej świadome decyzje oparte na faktach, co prowadzi do lepszego zarządzania zasobami i optymalizacji procesów logistycznych. Warto również zaznaczyć, że wdrożenie Przemysłu 4.0 przyczynia się do zwiększenia bezpieczeństwa pracy dzięki zastosowaniu zaawansowanych systemów monitorowania oraz robotyzacji niebezpiecznych czynności.
Jakie wyzwania stoją przed firmami w erze Przemysłu 4.0
Mimo licznych korzyści płynących z wdrożenia rozwiązań związanych z Przemysłem 4.0, przedsiębiorstwa muszą stawić czoła wielu wyzwaniom związanym z tą transformacją. Jednym z głównych problemów jest konieczność inwestycji w nowoczesne technologie oraz infrastrukturę IT, co może być dużym obciążeniem finansowym dla wielu firm, zwłaszcza tych mniejszych. Dodatkowo istnieje potrzeba przeszkolenia pracowników w zakresie obsługi nowych systemów oraz technologii, co wiąże się z czasem i kosztami związanymi z edukacją personelu. Kolejnym wyzwaniem jest zapewnienie odpowiedniego poziomu bezpieczeństwa danych oraz ochrony przed cyberatakami, które stają się coraz bardziej powszechne w erze cyfryzacji przemysłu. Firmy muszą również radzić sobie z problemem integracji różnych systemów oraz technologii, aby stworzyć spójną i efektywną sieć komunikacyjną między urządzeniami i procesami produkcyjnymi.
Jak Przemysł 4.0 wpływa na zatrudnienie i umiejętności pracowników
Wprowadzenie rozwiązań związanych z Przemysłem 4.0 ma znaczący wpływ na rynek pracy oraz wymagane umiejętności pracowników. Automatyzacja i robotyzacja procesów produkcyjnych mogą prowadzić do redukcji miejsc pracy w niektórych sektorach, zwłaszcza tych, które opierają się na rutynowych zadaniach. Jednak równocześnie pojawiają się nowe możliwości zatrudnienia w obszarach związanych z technologią, takich jak programowanie, analiza danych czy zarządzanie systemami informatycznymi. Pracownicy muszą dostosować się do zmieniającego się środowiska pracy, co wiąże się z koniecznością ciągłego kształcenia i rozwijania nowych umiejętności. W związku z tym wiele firm inwestuje w programy szkoleniowe oraz współpracuje z uczelniami wyższymi, aby przygotować przyszłych pracowników do wymagań rynku. Kluczowe staje się również rozwijanie umiejętności miękkich, takich jak zdolność do pracy w zespole, kreatywność oraz umiejętność rozwiązywania problemów. W miarę jak technologia staje się coraz bardziej zaawansowana, rośnie znaczenie kompetencji interpersonalnych, które są niezbędne do efektywnej współpracy w złożonych środowiskach produkcyjnych.
Jakie są przykłady zastosowania Przemysłu 4.0 w różnych branżach
Przemysł 4.0 znajduje zastosowanie w wielu branżach, przynosząc innowacje i poprawiając efektywność procesów produkcyjnych. W sektorze motoryzacyjnym wykorzystanie technologii IoT pozwala na monitorowanie stanu pojazdów w czasie rzeczywistym oraz przewidywanie awarii, co zwiększa bezpieczeństwo użytkowników i obniża koszty serwisowania. W branży spożywczej automatyzacja procesów pakowania oraz śledzenia produktów w łańcuchu dostaw przyczynia się do zwiększenia efektywności operacyjnej oraz poprawy jakości żywności. Z kolei w sektorze farmaceutycznym zastosowanie sztucznej inteligencji w badaniach nad nowymi lekami pozwala na szybsze odkrywanie skutecznych terapii oraz optymalizację procesów produkcyjnych. W przemyśle tekstylnym technologie druku 3D umożliwiają tworzenie spersonalizowanych produktów oraz zmniejszenie odpadów materiałowych poprzez precyzyjne dopasowanie do potrzeb klientów. Również branża budowlana korzysta z rozwiązań Przemysłu 4.0, implementując inteligentne systemy zarządzania projektami oraz wykorzystując drony do monitorowania postępu prac budowlanych.
Jakie są trendy rozwoju Przemysłu 4.0 na przyszłość
Przemysł 4.0 jest dynamicznie rozwijającym się obszarem, który będzie kształtował przyszłość produkcji i technologii przez wiele lat. Jednym z kluczowych trendów jest dalsza integracja sztucznej inteligencji w procesach produkcyjnych, co pozwoli na jeszcze większą automatyzację oraz optymalizację działań przedsiębiorstw. W miarę jak AI staje się coraz bardziej zaawansowana, jej zastosowanie będzie obejmować nie tylko analizę danych, ale także podejmowanie decyzji strategicznych w czasie rzeczywistym. Kolejnym istotnym trendem jest rozwój technologii blockchain, która ma potencjał do zwiększenia transparentności i bezpieczeństwa transakcji w łańcuchu dostaw, co jest szczególnie ważne w kontekście globalizacji rynku. Również Internet Rzeczy będzie nadal ewoluował, umożliwiając jeszcze szerszą komunikację między urządzeniami oraz zbieranie danych o wydajności procesów produkcyjnych. Warto również zwrócić uwagę na rosnącą rolę zrównoważonego rozwoju i ekologicznych rozwiązań w przemyśle, co skłoni firmy do inwestowania w technologie zmniejszające ich wpływ na środowisko naturalne.
Jakie są najlepsze praktyki wdrażania Przemysłu 4.0
Aby skutecznie wdrożyć rozwiązania związane z Przemysłem 4.0, przedsiębiorstwa powinny kierować się kilkoma najlepszymi praktykami, które pomogą im osiągnąć zamierzone cele. Po pierwsze, kluczowe jest przeprowadzenie dokładnej analizy potrzeb i możliwości firmy przed rozpoczęciem procesu transformacji cyfrowej. Zrozumienie specyfiki działalności oraz identyfikacja obszarów wymagających poprawy pozwoli na skoncentrowanie wysiłków na najważniejszych aspektach wdrożenia technologii 4.0. Po drugie, warto zaangażować pracowników na każdym etapie procesu transformacji, aby zapewnić ich wsparcie oraz zdobyć cenne informacje zwrotne dotyczące funkcjonowania nowych systemów. Szkolenia i warsztaty dla personelu są niezbędne do rozwijania umiejętności potrzebnych do obsługi nowoczesnych technologii oraz adaptacji do zmieniającego się środowiska pracy. Kolejnym krokiem jest stworzenie elastycznej infrastruktury IT, która umożliwi integrację różnych systemów oraz łatwe skalowanie rozwiązań w miarę potrzeb firmy.
Jakie są perspektywy dla Przemysłu 4.0 w Polsce
Polska ma ogromny potencjał do rozwoju Przemysłu 4.0 dzięki silnej bazie przemysłowej oraz rosnącemu zainteresowaniu nowoczesnymi technologiami ze strony przedsiębiorców i instytucji badawczych. W ostatnich latach wiele polskich firm zaczęło inwestować w automatyzację procesów produkcyjnych oraz cyfryzację swoich działań, co przyczynia się do zwiększenia konkurencyjności na rynku europejskim i globalnym. Rządowe programy wspierające innowacje oraz rozwój technologii również sprzyjają transformacji przemysłowej w kraju, oferując dotacje i ulgi podatkowe dla przedsiębiorstw inwestujących w nowoczesne rozwiązania technologiczne. Polska może stać się liderem w regionie Europy Środkowo-Wschodniej pod względem wdrażania rozwiązań związanych z Przemysłem 4.0 dzięki współpracy między sektorem prywatnym a instytucjami naukowymi oraz edukacyjnymi, które kształcą przyszłych specjalistów w dziedzinie nowych technologii.
Jakie są kluczowe wyzwania dla Polski w kontekście Przemysłu 4.0
Mimo że Polska ma wiele atutów sprzyjających rozwojowi Przemysłu 4.0, istnieją również istotne wyzwania, które mogą hamować postęp w tej dziedzinie. Jednym z głównych problemów jest niedobór wykwalifikowanej kadry pracowniczej zdolnej do obsługi nowoczesnych technologii oraz systemów informatycznych stosowanych w przemyśle 4.0. Firmy muszą inwestować nie tylko w nowe technologie, ale także w rozwój kompetencji swoich pracowników poprzez szkolenia i kursy zawodowe, aby sprostać wymaganiom rynku pracy. Kolejnym wyzwaniem jest konieczność modernizacji infrastruktury IT wielu polskich przedsiębiorstw, które często korzystają z przestarzałych systemów informatycznych utrudniających integrację nowych technologii z istniejącymi procesami produkcyjnymi.