Destylacja rozpuszczalników to proces, który odgrywa kluczową rolę w chemii i przemyśle chemicznym. Polega on na oddzieleniu składników mieszaniny na podstawie różnic w ich temperaturach wrzenia. W praktyce oznacza to, że gdy mieszanina jest podgrzewana, składnik o niższej temperaturze wrzenia paruje jako pierwszy, a następnie skrapla się w chłodnicy, tworząc czystszy produkt. Proces ten można przeprowadzać na różne sposoby, w tym destylację prostą, frakcyjną oraz destylację z wykorzystaniem kolumny destylacyjnej. W przypadku destylacji rozpuszczalników szczególnie ważne jest, aby zrozumieć właściwości fizyczne i chemiczne substancji, które chcemy oddzielić. Właściwy dobór sprzętu oraz parametrów procesu ma kluczowe znaczenie dla uzyskania wysokiej czystości końcowego produktu.
Jakie są zastosowania destylacji rozpuszczalników w przemyśle
Destylacja rozpuszczalników znajduje szerokie zastosowanie w różnych gałęziach przemysłu, od farmaceutycznego po petrochemiczny. W przemyśle farmaceutycznym proces ten jest wykorzystywany do oczyszczania substancji czynnych oraz rozpuszczalników używanych w produkcji leków. Dzięki destylacji możliwe jest uzyskanie wysokiej czystości substancji, co jest kluczowe dla zapewnienia skuteczności i bezpieczeństwa leków. W przemyśle petrochemicznym destylacja służy do separacji różnych frakcji ropy naftowej, takich jak benzyna, olej napędowy czy nafta. Każda z tych frakcji ma swoje specyficzne zastosowanie i właściwości. Ponadto, destylacja rozpuszczalników jest również stosowana w produkcji alkoholu oraz w laboratoriach chemicznych do oczyszczania reagentów i rozpuszczalników organicznych.
Jakie są najczęstsze metody destylacji rozpuszczalników
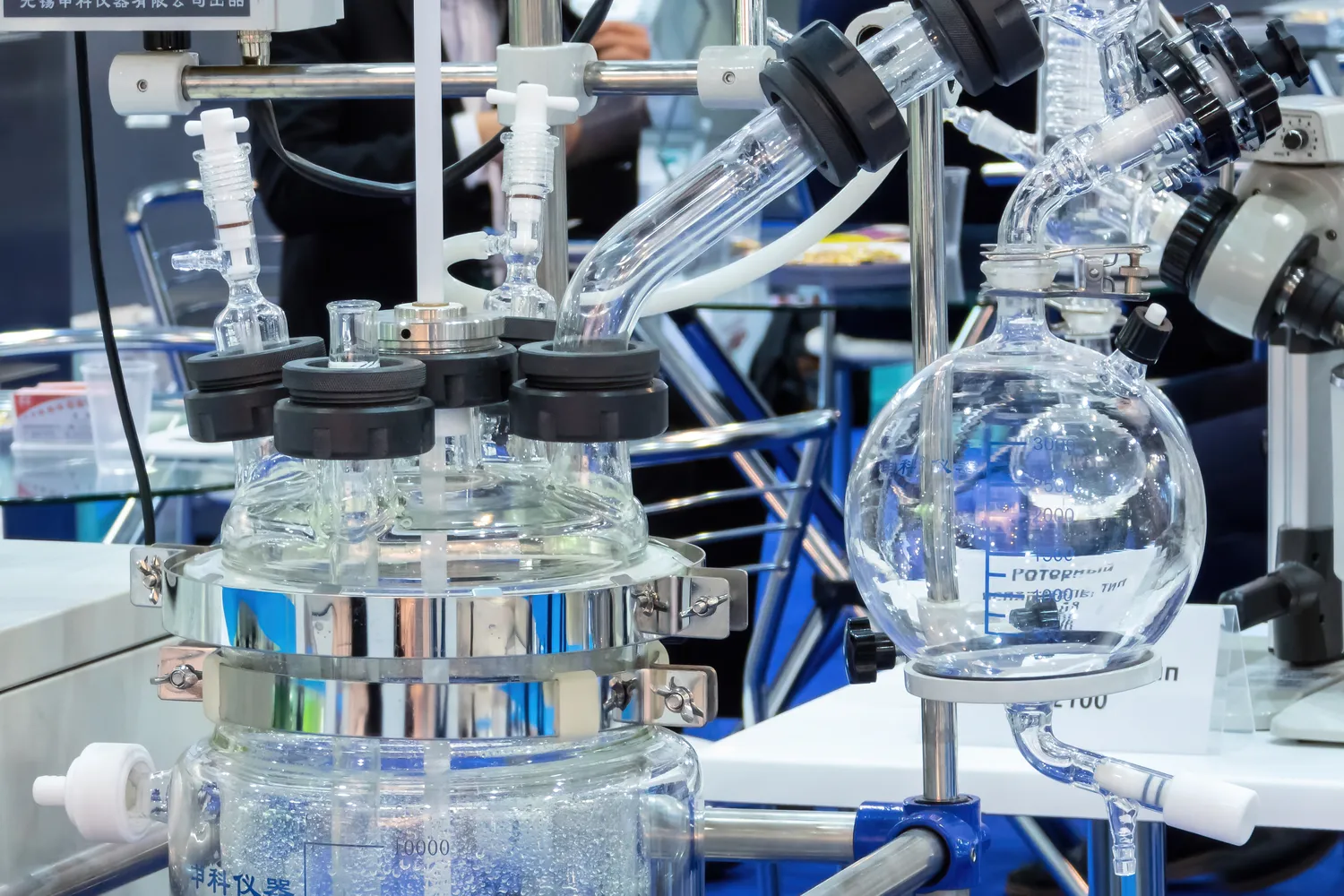
W dziedzinie destylacji rozpuszczalników wyróżnia się kilka podstawowych metod, które są stosowane w zależności od charakterystyki mieszaniny oraz wymaganej czystości produktu końcowego. Najpopularniejszą metodą jest destylacja prosta, która polega na jednorazowym podgrzewaniu mieszaniny i skraplaniu pary. Jest to proces stosunkowo łatwy do przeprowadzenia i często wykorzystywany w laboratoriach do oczyszczania niewielkich ilości substancji. Kolejną metodą jest destylacja frakcyjna, która pozwala na bardziej efektywne oddzielanie składników o zbliżonych temperaturach wrzenia dzięki zastosowaniu kolumny frakcyjnej. Ta metoda jest szczególnie przydatna w przemyśle chemicznym, gdzie wymagana jest wysoka czystość produktów. Istnieją także bardziej zaawansowane techniki, takie jak destylacja azeotropowa czy destylacja pod ciśnieniem atmosferycznym lub próżniowym, które umożliwiają separację składników trudnych do oddzielenia za pomocą tradycyjnych metod.
Jakie są wyzwania związane z procesem destylacji rozpuszczalników
Proces destylacji rozpuszczalników wiąże się z wieloma wyzwaniami technicznymi i ekonomicznymi, które mogą wpływać na jego efektywność i opłacalność. Jednym z głównych problemów jest konieczność dokładnego monitorowania temperatury i ciśnienia podczas całego procesu, co wymaga zaawansowanego sprzętu pomiarowego oraz systemów kontroli. Niewłaściwe ustawienia mogą prowadzić do strat materiałowych lub obniżenia jakości końcowego produktu. Kolejnym wyzwaniem jest zarządzanie dużymi ilościami energii potrzebnymi do podgrzewania mieszanin oraz chłodzenia skroplin. Optymalizacja tych procesów może znacząco wpłynąć na koszty operacyjne zakładów przemysłowych. Dodatkowo, niektóre mieszaniny mogą tworzyć azeotropy, co utrudnia ich separację za pomocą standardowych metod destylacji. W takich przypadkach konieczne może być zastosowanie dodatkowych technik separacyjnych lub modyfikacja warunków procesu.
Jakie są kluczowe czynniki wpływające na efektywność destylacji rozpuszczalników
Efektywność procesu destylacji rozpuszczalników zależy od wielu czynników, które mogą znacząco wpłynąć na jakość i ilość uzyskanego produktu. Jednym z najważniejszych aspektów jest temperatura wrzenia poszczególnych składników mieszaniny. Różnice w temperaturach wrzenia pozwalają na skuteczne oddzielanie substancji, jednak zbyt bliskie wartości mogą prowadzić do trudności w separacji. W takim przypadku konieczne może być zastosowanie destylacji frakcyjnej, która umożliwia lepsze rozdzielenie składników. Kolejnym kluczowym czynnikiem jest ciśnienie, które wpływa na temperaturę wrzenia substancji. W obniżonym ciśnieniu temperatura wrzenia spada, co może być korzystne w przypadku substancji wrażliwych na wysoką temperaturę. Dodatkowo, rodzaj użytej kolumny destylacyjnej oraz jej konstrukcja mają istotny wpływ na efektywność procesu. Kolumny o większej liczbie teoretycznych półek pozwalają na lepsze rozdzielenie składników, co przekłada się na wyższą czystość produktu końcowego.
Jakie są innowacje technologiczne w dziedzinie destylacji rozpuszczalników
W ostatnich latach w dziedzinie destylacji rozpuszczalników pojawiło się wiele innowacji technologicznych, które mają na celu zwiększenie efektywności i bezpieczeństwa tego procesu. Jednym z trendów jest rozwój nowoczesnych systemów automatyzacji, które umożliwiają precyzyjne monitorowanie i kontrolowanie parametrów procesu w czasie rzeczywistym. Dzięki zastosowaniu zaawansowanych czujników oraz systemów informatycznych możliwe jest szybkie reagowanie na zmiany warunków pracy, co przekłada się na lepszą jakość produktów oraz mniejsze straty materiałowe. Innym kierunkiem innowacji jest wykorzystanie nowych materiałów do budowy kolumn destylacyjnych, takich jak nanomateriały czy materiały kompozytowe, które charakteryzują się lepszymi właściwościami termicznymi i chemicznymi. Ponadto, rozwijane są technologie związane z destylacją membranową oraz ekstrakcją cieczy cieczą, które mogą stanowić alternatywę dla tradycyjnych metod destylacji. Te nowoczesne podejścia mogą przyczynić się do zmniejszenia zużycia energii oraz poprawy wydajności procesów separacyjnych.
Jakie są różnice między destylacją a innymi metodami separacji
Destylacja rozpuszczalników to jedna z wielu metod separacji składników mieszanin, a jej skuteczność i zastosowanie różnią się od innych technik. Na przykład, ekstrakcja cieczy cieczą polega na wykorzystaniu różnicy w rozpuszczalności składników w różnych rozpuszczalnikach, co może być korzystne w przypadku substancji o podobnych temperaturach wrzenia. Ta metoda często wymaga mniej energii niż destylacja i może być stosowana do separacji substancji organicznych lub nieorganicznych. Z kolei chromatografia to technika oparta na różnicach w adsorpcji składników na stałym nośniku, co pozwala na bardzo precyzyjne oddzielanie substancji nawet o zbliżonych właściwościach chemicznych. Jest to metoda często stosowana w laboratoriach analitycznych do identyfikacji i oczyszczania związków chemicznych. Inna technika to filtracja, która polega na oddzielaniu ciał stałych od cieczy lub gazu za pomocą porowatego materiału filtracyjnego.
Jakie są aspekty bezpieczeństwa związane z destylacją rozpuszczalników
Bezpieczeństwo podczas procesu destylacji rozpuszczalników jest kluczowym zagadnieniem zarówno w laboratoriach, jak i w zakładach przemysłowych. Ze względu na wysokie temperatury oraz obecność lotnych substancji chemicznych istnieje ryzyko pożaru lub eksplozji. Dlatego niezwykle ważne jest przestrzeganie zasad BHP oraz stosowanie odpowiednich środków ochrony osobistej przez pracowników. Właściwe wentylowanie pomieszczeń roboczych oraz stosowanie systemów detekcji gazów mogą znacznie zmniejszyć ryzyko wystąpienia niebezpiecznych sytuacji. Dodatkowo, należy zwrócić uwagę na odpowiednie przechowywanie substancji chemicznych oraz ich transport wewnętrzny, aby uniknąć przypadkowego uwolnienia toksycznych oparów czy wycieków. W kontekście procesów przemysłowych istotne jest także regularne przeprowadzanie przeglądów technicznych urządzeń oraz szkoleń dla personelu dotyczących obsługi sprzętu i reagowania w sytuacjach awaryjnych.
Jakie są przyszłe kierunki badań nad destylacją rozpuszczalników
Przyszłość badań nad destylacją rozpuszczalników zapowiada się obiecująco dzięki rosnącemu zainteresowaniu efektywnością energetyczną oraz ekologicznymi aspektami procesów chemicznych. Naukowcy poszukują nowych sposobów optymalizacji procesów destylacyjnych poprzez zastosowanie technologii komputerowych i symulacji numerycznych, które pozwalają na modelowanie zachowań mieszanin i przewidywanie wyników różnych konfiguracji sprzętowych. Badania nad nowymi materiałami do budowy kolumn destylacyjnych również stają się coraz bardziej popularne; nanomateriały czy materiały o zmiennej porowatości mogą przyczynić się do zwiększenia wydajności procesów separacyjnych. Ponadto rozwijane są technologie związane z recyklingiem rozpuszczalników oraz odzyskiwaniem ciepła odpadowego z procesów destylacyjnych, co może znacząco wpłynąć na redukcję kosztów operacyjnych oraz zmniejszenie wpływu przemysłu chemicznego na środowisko naturalne.
Jakie są najczęstsze błędy popełniane podczas destylacji rozpuszczalników
Prowadzenie procesu destylacji rozpuszczalników wymaga dużej precyzji i znajomości zasad działania sprzętu, dlatego też wiele osób popełnia typowe błędy, które mogą negatywnie wpłynąć na wyniki eksperymentu lub produkcji przemysłowej. Jednym z najczęstszych błędów jest niewłaściwe ustawienie temperatury podgrzewania mieszanki; zbyt wysoka temperatura może prowadzić do niekontrolowanego parowania i strat materiałowych, natomiast zbyt niska może skutkować niepełnym oddzieleniem składników. Kolejnym problemem jest brak odpowiedniego monitorowania ciśnienia wewnętrznego systemu; zmiany ciśnienia mogą wpływać na temperatury wrzenia substancji i prowadzić do nieefektywnej separacji. Niewłaściwe przygotowanie sprzętu przed rozpoczęciem procesu również może skutkować problemami; niedokładne czyszczenie kolumny lub użycie nieodpowiednich materiałów eksploatacyjnych mogą prowadzić do kontaminacji produktu końcowego.